Randy I thought about welding the grab bar, but I am scared to get it tigged on because there is nothing there but the floor. What I drew up is the final design of the prototype that is on my boat now. The first pic is the assembly I am going to weld up. The second pic shows where it'll be in the boat. The grab bar I have now is on the back side of the second seat and it is too close. I am going to put it on the front side. Also the angle iron will be longer across the seat to distribute the force more evenly. The larger pipe will be welded to the angle iron and bolted onto the seat as one unit. I want the female pipe to be flush so if the grab bar is out you can still use the seat. I aim to weld it up tight enough so no pins are required for removal, or attempt to. I never put any upward pressure on my grab bar, but if I feel the need for pins to be inserted I will. I will just have to see. I am not working with much to attach to, and the largest most stable point near my driving location is that seat. Luckily, it is the seat least used in the boat. I think it will be plenty stout with the female pipe running almost to the floor. I am going to weld up the bottom of the female pipe to keep the male pipe from scraping the bottom of the hull. I hope it works because I don't feel comfortable getting the thin ga aluminum welded on. I may have to rig up some sort of plate and weld the bottom of the female pipes to it then screw the plate down to the ribs. I just don't want to add too much extra weight as I have to be able to slide this rig off of a trailer if need be.
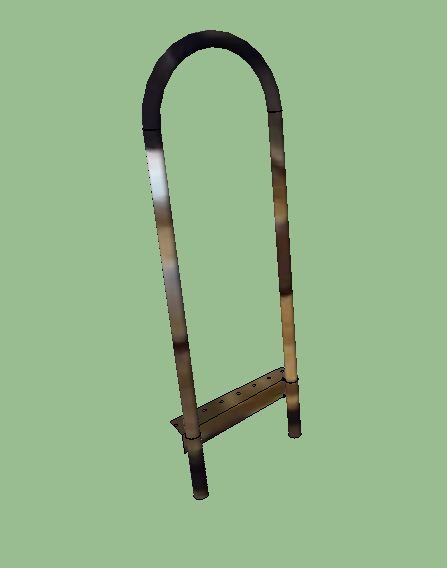
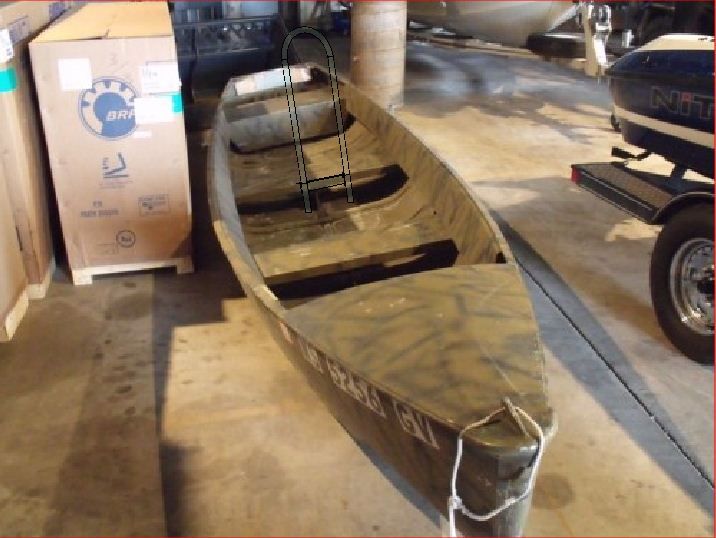
I have a 9 hp MB longtail on it now so I have gotten a few hours of stick time to decide what I want. The 9 hp is a dude in that boat with me. It'll run right at 13. Which is fine speeds for a longtail. But what I want is slow speed "umph" to get up and over stuff, and that 9 hp on that long, skinny, 110lb hull is the best match out there, save a custom made skiff. When I put my buddy who is 6'8" 290 lbs, Angus who is 80, a full yeti and various other items it ran...right at 13 mph. Those hulls are just weird to the everyday man like me familiar with bateaus and planing hulls. I will say one thing- the rig slid off of stumps, cypress knees, grass, anything. My girlfriend's brother has a 14 foot Phowler Prowler with an 18 hp copperhead that'll run like a scalded dog, 33 mph with me and him in there. And it is a small, light rig. He went everywhere I did, but with much more trouble due to the low water conditions and the stumps. I hardly ever got over idle and when going over large beaver dams I'd shower down and it's scoot right over. It does way better than the 13 hp I had on a 1436. That dude is made for the swamp. And just like a skiff, it made cutting through the buck brush thickets and tupelo brakes a much more enjoyable experience, if it ever has been. I am going to use some of your ideas to keep the floor space clean, which is hard to do in a small rig. I don't plan on hunting out of it, but we are investing in a couple of those putt hut blinds and are hoping they will make life easier in the thicket.
The 100 lb motor doesn't even budge the transom, which is 25 inches wide. But the main problem is the round chines coupled with the heavier motor make the rig slide at idle speeds. And the kicker is idle speed in that rig is pretty much planing speed for a SB which is technically around 6 mph. And also the motor is not easily removeable like some of the other smaller motors.
With that being said I am going to sell the motor and go even lighter. I have several places that will require me to remove the rig from the trailer and slide in. Also in the swamp, for the majority of the year, the water level is down below the low water crossings. At most times of the year you would have to pull your rig up and over 3 feet high chert gravel roads. This is good news if we hunt holes where access is walk in only because boats can't get over them. But bad news when the walk in is as deltadukman put it on another thread, a death march.